3 Phase Delta vs. Wye: Key Differences and Applications
Understanding the differences between 3 phase Delta and Wye configurations is crucial for engineers and technicians who deal with electrical power distribution and equipment. Each configuration has its unique characteristics and is suitable for specific applications. This brief exploration will highlight the key distinctions and typical uses of Delta and Wye configurations in three-phase systems.
Key Distinctions and Applications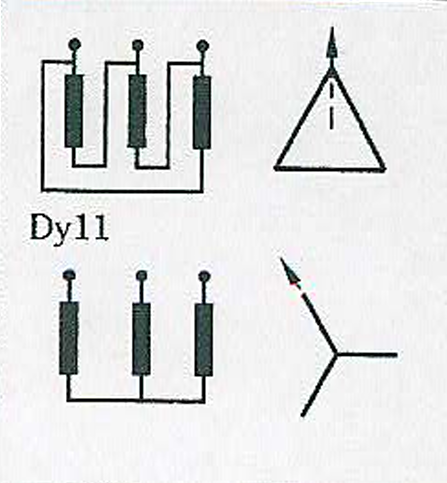
The Delta configuration features a closed loop with each phase connected end-to-end, forming a triangle-like shape. This setup is known for its ability to provide redundancy; if one phase fails, the other two can continue to operate, which enhances system reliability. Delta configurations are typically used in applications requiring high starting torque, such as heavy machinery and industrial motors. They are also preferred where the load requires higher phase-to-phase voltage levels.
On the other hand, the Wye (or Star) configuration connects each phase to a common central point, which may or may not be grounded. This setup provides a neutral point and allows the use of both phase-to-neutral and phase-to-phase voltages, making it versatile for different types of electrical loads. Wye configurations are commonly used in general power distribution and in systems where safety is paramount, as they provide a neutral path for fault currents, enhancing overall system safety.
In summary, the choice between Delta and Wye configurations depends on specific power requirements, desired system stability, and safety considerations. Each has its advantages that can be leveraged according to the needs of the application.